Return to Menu
ADVANTAGES OF THE MITSUBISHI PROCESS
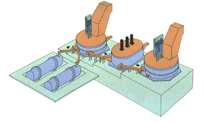
1. Process Advantages
- Continuous and stable furnace operations
-> Enables simple and optimum operator control.
- High oxygen utilization and good heat transfer in smelting and converting operations, by virtue
of the high intensity reaction zone directly below the furnace lances.
- Long furnace life by keeping the constant and stable melt level except the reaction zone below the lances.
- Rapid melting of the S furnace feed materials and quick formation of a consistent and high grade
copper matte. In practice, the matte grade can be accurately controlled between 60 and 70 % Cu, by adjusting
the blowing rate through lances.
- Stable and continuous conversion of copper
matte to blister copper, as a result of consistent matte flow and grade, good coolant control, the high intensity
reaction zone below the lances, and the use of limestone as flux.
- Efficient capture of feed particulates into the melt, with little carry-over of unsmelted dust
to the waste heat boiler and precipitator. In practice the amount of dust removed at
the S boiler relates more to fluctuations in the volatile components of the copper
concentrates than to their feed rate. Only 2 to 5 % of the total solid feeds to the
S furnace report to the waste heat boiler. In the C furnace the dust carry-over is much lower.
- Flexibility in treating a wide range and grade of concentrates and changing feed rate
by the use of multiple lance system.
- Flexibility in treating many secondary materials while keeping good environment.
Refinery anode scrap and purchased scrap can be automatically charged and treated
in the C furnace by using the excess heat of the furnace.
- Low copper content is in discard slag (0.6 to 0.8 % Cu). This is lower than other processes, where
dirty operations such as slag grinding and flotation have to be employed, or large amounts
of molten slag have to be recycled in the smelting or settling furnaces to avoid costly copper losses.
- Low atmospheric emissions, particularly sulphur dioxide bearing, than any other copper smelting and converting
process.
- Allowance for compact and standard design of acid plant. This contrasts sharply with other processes,
where enormous variations in gas flowrate and strength mandate the use of larger and
less efficient custom-designed acid plants. Also continuous nature of off-gas also reduces
maintenance costs at the acid plant including the cost of screening catalysts.
- Clean workspace conditions. This stems directly from the continuous
nature of the furnace operations and the elimination of ladle transfers and other
batch type operations. The totally encapsulated furnaces with their small side-wall outlets
and the use of covered launders further simplifies plant ventilation requirements.
- Minimal cost requirements. The need for costly foundations is reduced
due to small but highly efficient furnace design. Furthermore pneumatic feed systems
and short launders, reduce the required building area for new smelter installations, and refit
modifications. Also plant metal inventories are reduced, since only short furnace retention
times are required.
- Minimal space requirements. Compact furnace design, short launders,
and pneumatic feed systems, reduce the building area required for new smelter installations,
and refit modifications.The following figure shows the actual layout of the new Mitsubishi
Process plant at Naoshima, comprising feed preparation, the continuous furnace line
with its associated gas cooling and cleaning equipment, and anode casting. Also shown
are the much larger areas occupied by the various sections of the now abolished older
conventional smelter. The figure dramatically illustrates the highly functional and extremely
compact layout of the Mitsubishi Process, which in this particular case, is treating
almost three times the concentrates formerly handled by the now abolished conventional smelter.
* Layout of the new Mitsubishi Process Plant
and the now abolished conventional smelter
at Naoshima *
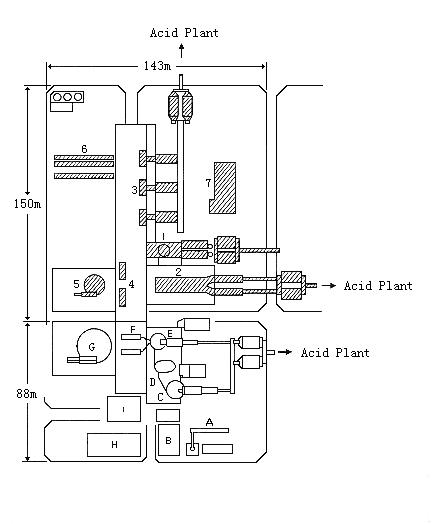 |
Abolished Conventional Smelter (hatched)
- 108,000 MT/Y -
1.Fluo-solid Roaster
2.Reverberatory Furnace
3.P-S Converter
4.Anode Furnace
5.Casting Wheel
6.Converter Slag Conveyor
7.Compressor House
New Mitsubishi Process Plant - 270,000
MT/Y
-
A.Conc.Dryer
B.Storage Bin
C.Smelting Furnace
D.Slag Cleaning Furnace
E.Converting Furnace
F.Anode Furnace
G.Casting Wheel
H.Compressor House
I.Control Room |
* Layout of Gresik plant whose capacity reached to 300,000 tpy copper in 2009. *
2. Cost Advantages
The following table provides an indexed comparison
between the Mitsubishi Process and other
processes which are combined with conventional
P-S converters.
The figures are based on studies carried
out by various international engineering
companies and Mitsubishi Materials's own
internal cost data. Taking the Mitsubishi
Process to be 100, the table compares the
average costs of different processes, and
makes appropriate adjustments for batch converting,
slag grinding and flotation, the treatment
of fugitive emission and so on.
* Indexed Cost Comparison *
|
Mitsubishi Process |
Other Processes (Average) |
Capital Cost (*1)
(Excluding Refinery Costs)
|
100
(100) |
105 - 120
(106 - 122) |
Operating Cost
Manpower(*2)
Fuel Oil(*2)
Coal(*2)
Oxygen(*2)
Maintenance(*2)
Purchased Power(*1)(*3)
Total Off Gas Vol.(*2) |
100
100
100
100
100
100
100 |
130 - 140
90 - 130
100 - 120
80 - 90
120 - 130
90 - 110
120 - 200 |
*1 Including smelter, slag flotation plant,
oxygen plant, acid plant,
fugitive gas treatment plant and refinery
*2 Smelter and slag flotation plant
*3 Purchased power = Actual consumption -
Turbine generated power, using the
waste heat boiler steam
In the other continuous converters to treat solid matte, the matte melt should be
granulated by a large amount of water, screened, crushed and mechanically transported,
and for converting the solid matte should be dried or pelletized (adding water),
and a large amount of additional energy (fuel and/or oxygen) is necessary. Furthermore,
for treating refinery anode scrap and purchased scrap, the additional furnace and fuel
would be necessary although the big converter aisle and overhead crane would be unnecessary.
Accordingly, the construction and operating cost would be higher than the Mitsubishi process.
Return to Menu