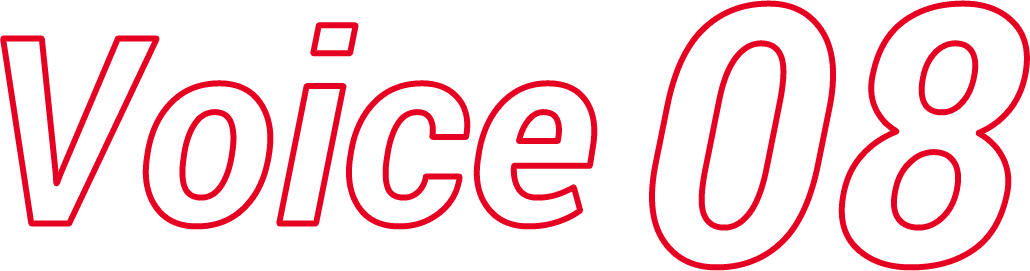
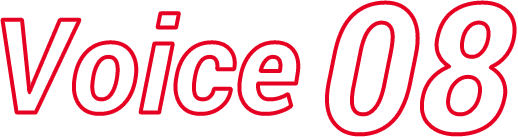
金属事業カンパニー
初めてのインドネシア。
投資総額250億円の
ビッグプロジェクトに挑む。
- I.K
-
PT.Smelting
(金属事業カンパニー/インドネシア)2011年入社
※所属部署・役職、インタビュー内容は当時のものです
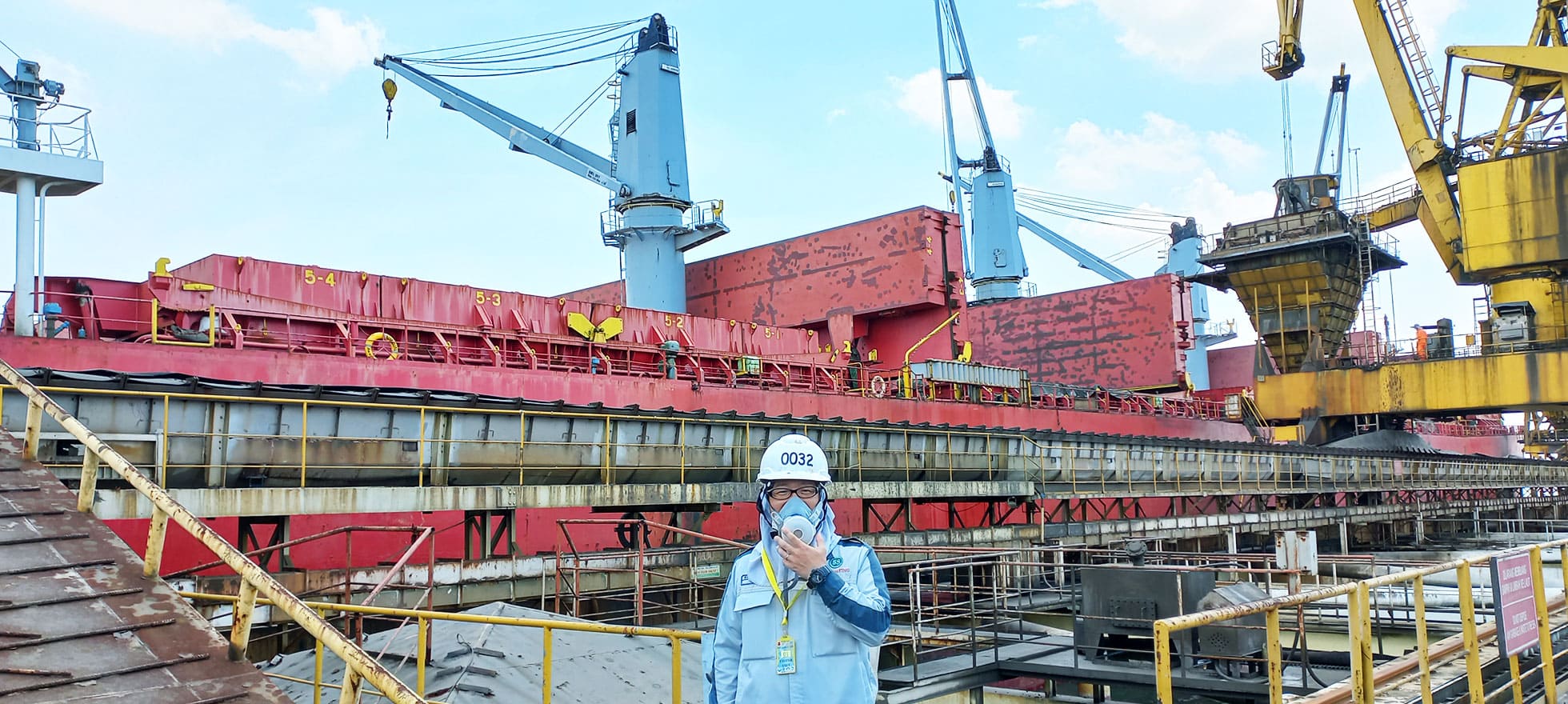
ものづくりの最先端を学んだ
直島製錬所での10年間。
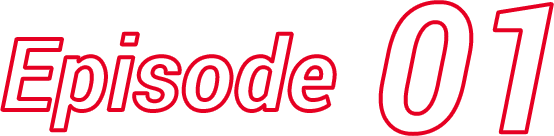
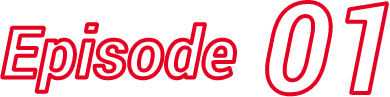
大学院では化学工学を専攻、プラズマ内の特殊な環境で起こる化学反応について研究していました。就職に際しては、ものづくりの実際のプロセスに関わる仕事がしたいと考え、化学メーカーや素材メーカーでの設備設計業務をイメージしながら企業を絞り込んでいきました。曽祖父の代から三菱系の企業には縁があったことから、三菱マテリアルにも親近感を感じて説明会に参加しました。企業概要の紹介が終わると、採用担当の方が「ほかにも知りたいことはありますか?」と声を掛けてくれ、プロセス関連の仕事について質問すると、興味深い話をいろいろとしてくれました。その応対ぶりから、人を大切にする姿勢や働きやすさを感じ取ることができました。
最初の配属先は直島製錬所の保全動力課で、生産設備のメンテナンス・修繕と新規に設備を導入する設備投資を担当しました。1年目の終盤から所内の製造現場の1つを任されて設備メンテナンスと設備投資に携わり、希望していた新規設備のプロセス設計から設置までの一連の業務に取り組むことができました。
以後10年間、直島で設備関係の業務経験を積んだ後、2021年7月、当社の海外銅製錬所であるインドネシアのPT.Smelting(以下、PTS)へ異動になりました。PTSは、直島の技術をベースとして1996年に誕生した製錬所で、当社が独自開発した「三菱連続製銅法」が導入されています。初の海外勤務での心配事は、私の英語がどのくらい通用するか?ということくらいで、元同僚や先輩もいるので不安材料はありませんでした。上司からは「やりがいのあるビッグプロジェクトが動く予定だから、しっかり学んで来い」と言われ、ステップアップの絶好のチャンスと勇んでインドネシアへ向かいました。
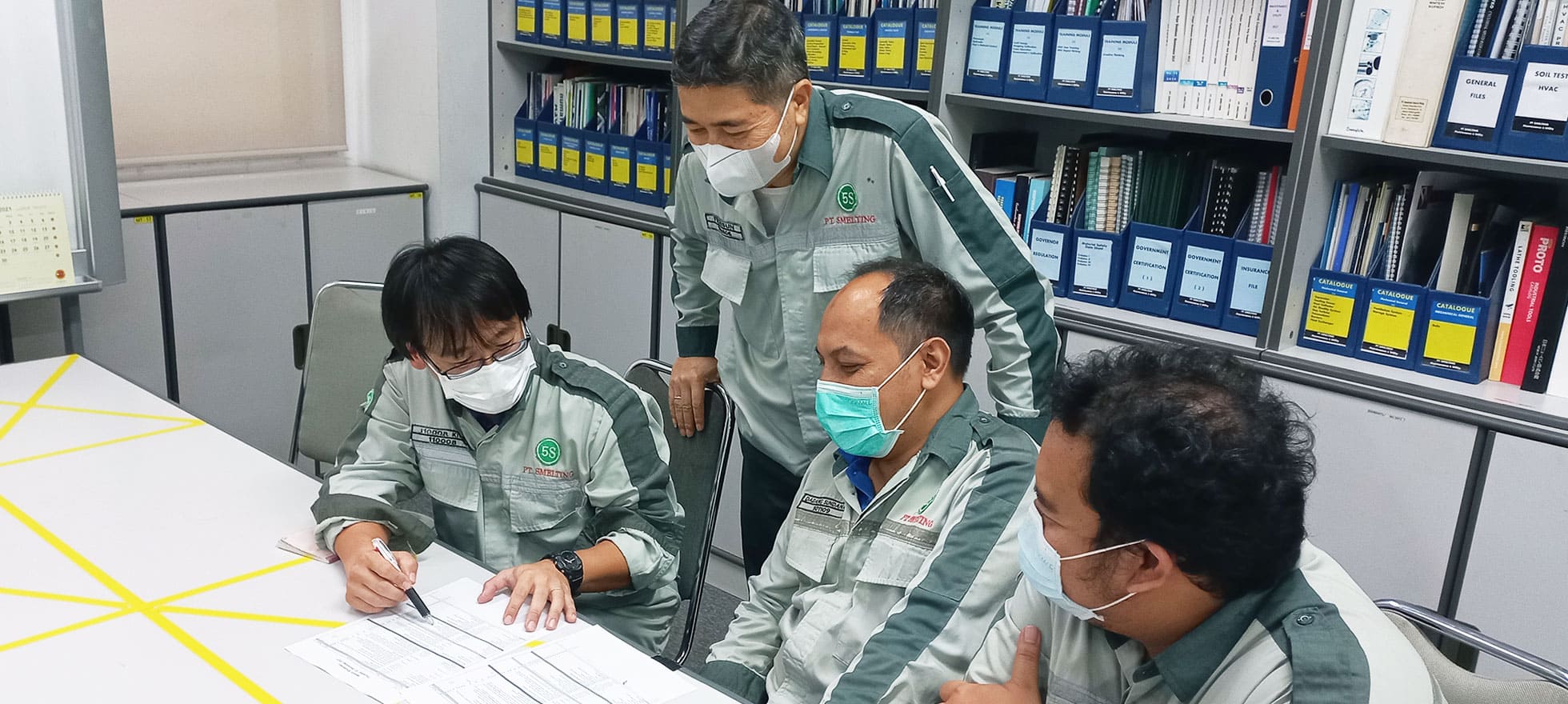
1ヵ月で500の工事を完了させた
経験を活かし、プロジェクトを前へ。
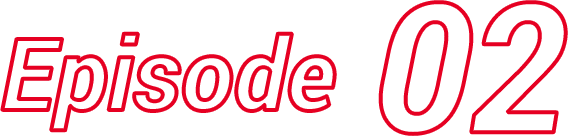
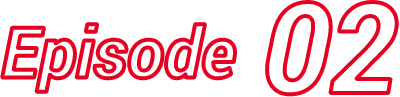
PTSでは、直島時代と同じく生産設備関連の業務に取り組むメンテナンス&ユーティリティー部門に所属し、「銅精鉱処理拡張プロジェクト」をメインに担当しています。ミッションは、2024年前半までに銅製錬の原料である銅精鉱の処理能力を現在の年間100万トンから130万トンへ増強し、電気銅の生産能力を年間30万トンから34万2,000トンに拡大することです。投資総額約250億円というビッグプロジェクトの予算管理、進捗管理、設備の詳細設計などプロジェクトマネジメント全般に取り組んでいます。
現在の業務の推進に当たっては、直島での「製銅炉 定期修理(炉修)」の経験が大いに役立っています。直島では2年に1回、1ヵ月ほど操業を停止して炉の補修を行います。このタイミングに合わせて、大型の設備導入や各種設備のメンテナンスも行います。「炉修」全体では、大小合わせて500近い工事を数十億円掛けて実施します。私は2017年にこの炉修工事の責任者を任され、予算管理から工事管理までの全てに取り組みました。
これだけの工事を1ヵ月で行うとなると、単純に工事を詰め込むだけでは作業や車両動線などの干渉が頻発します。そこで、全ての工事関係者がスムーズに且つストレスなく作業が進められるよう、工事担当者と私たち保全担当者、現場の操業担当者らが集合。作業時間、作業スペース、作業車と作業員の動線などについて細かく内容を確認・調整し、情報共有しながら工事を実施しました。それはまるで、500個の細かいピースを組み合わせ、「炉修」という巨大なジグソーパズルを完成させるような感覚でした。
今回PTSで担当するプロジェクトは、その数倍もの規模になります。関わる機器メーカー、エンジニアリング会社、建築・施工会社は、日本、カナダ、アメリカ、フィンランド、インドネシアと、グローバルに広がっています。各社と連携を図り、綿密に情報交換しながら、スムーズにプロジェクトを進めることの大変さは、想像もできないのが正直なところです。直島での経験を存分に活かし、強い信念を持ってこの大役を果たしていきたいと考えています。

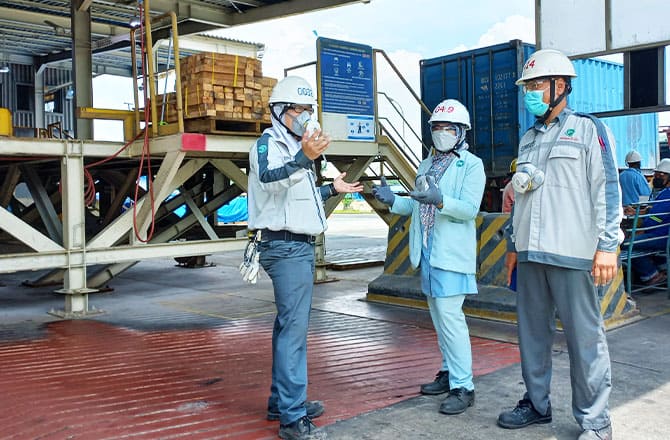
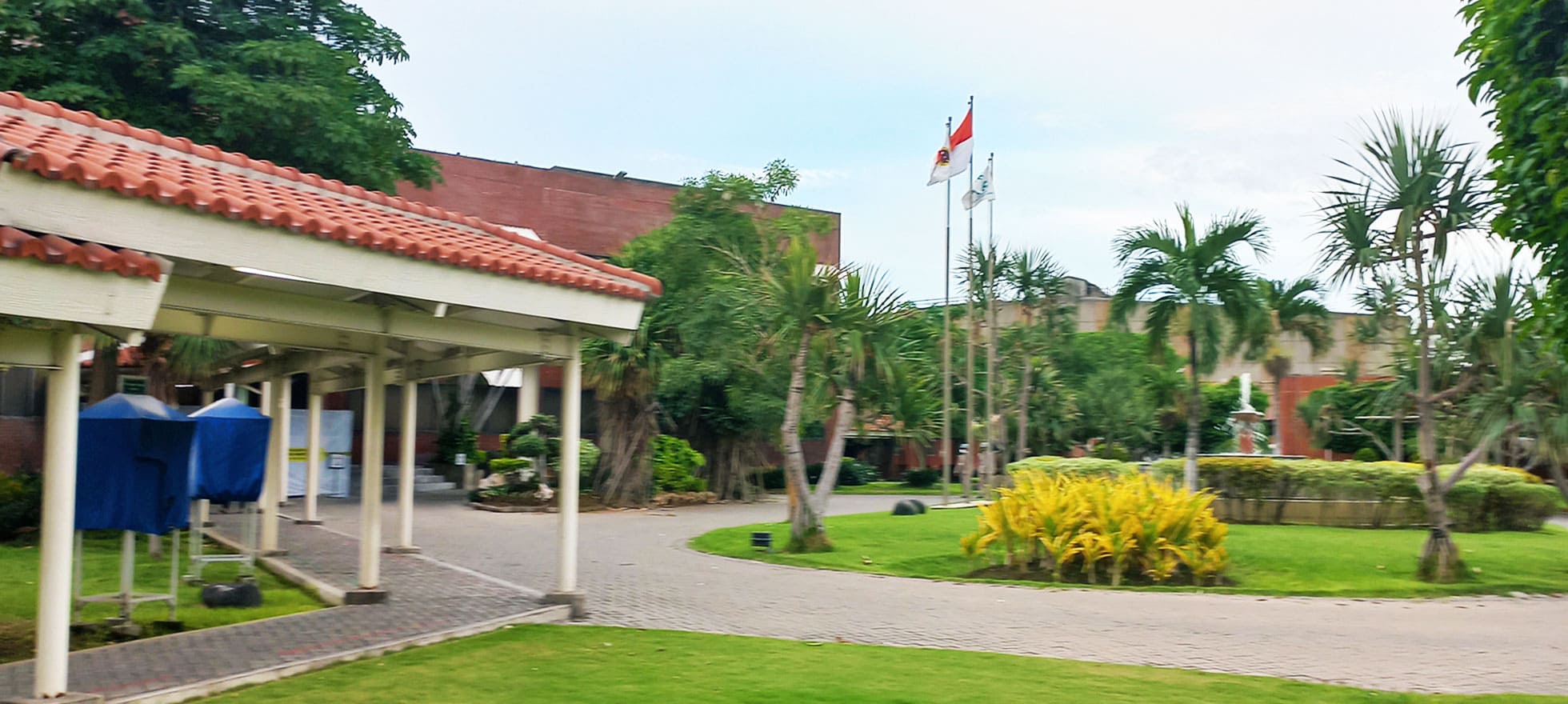
数十年先を見据えた
設備設計や情報管理を実現。
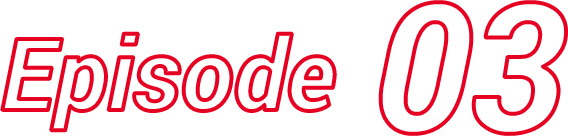
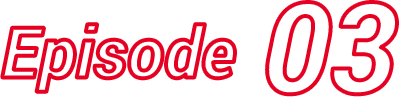
プロジェクトの推進に当たって強く意識しているのは、操業担当者に感謝される成果を導き出すことです。今回のプロジェクトで完成したラインを、PTSの方々は今後数十年間に亘って使用し、銅製錬に取り組んでいきます。その時、「本当に良いものを造ってくれた」と言ってもらえることが、設備に携わる者として最高に嬉しい瞬間になるはずです。
そのために重要なのは、現場の操業担当者との密接なコミュニケーションです。議論を重ねて設備に対する要望とその背景にある理由を把握し、設計思想に盛り込むことで、より良いプロセス・設備が完成します。
PTSには、国内と同様に業務フローや情報管理等の改善を常に図っていく文化が根付いています。今、提案したいと考えているのが、設計図面の整理・保管の徹底です。設立当初の図面はPTS内に整理・保管されていますが、以後の改造・改修図面は、業務を担当したグループ企業のエンジニアリング会社にあり設計図面が分散しています。
今後も長期に亘って操業を続けていく中で、設備の改修・増強のニーズは、必ず発生します。その際に業務がスムーズに且つストレスなく実施できるよう、ローカルの技術者を巻き込んで図面を社内で保管・整理するメリットを理解してもらい、その先のDX(Digital Transformation)化にも取り組んでいきたいと思います。

ある一日のスケジュール
-
- 7:00
- 出社して最初にメールチェック 夜中の作業報告にも目を通して工場全体の状況を把握
-
- 7:20
- 広場に集合して全員で体操 今日も1日安全に業務を進めることを確認
-
- 7:30
- メンテナンス&ユーティリティーのメンバーとのMorning Meetingで操業の状況や修繕・工事の進捗情報を共有
-
- 9:00
- マネージャー対象のMorning Meetingに参加して各部門の報告を聞いてPTS全体に関する情報を共有
-
- 9:30
- 担当案件の工事設計に着手
-
- 10:30
- 担当案件の状況を確認するために事務所から歩いて20分の現場へ向かう
-
- 11:40
- 事務所に戻って確認した内容を報告書にまとめる
-
- 12:00
- 昼食 日本からの出向者が全員集合 今日のメニューは日本料理屋の仕出し弁当
-
- 13:00
- メンテナンス&ユーティリティーのAfter Lunch Meetingを実施 午前中に確認した現場の状況を報告し合って今後の対応を検討
-
- 13:30
- 操業とミーティング プロジェクト案件の内容について直接会って確認
-
- 15:00
- 新規導入予定の日本装置メーカーとWeb Meeting 明日はフィンランドとカナダのメーカーとミーティングの予定
-
- 15:30
- 午前中とは別案件の現場へ 雨季は突然の降雨があることから雲行きが怪しくなってきたら早めに事務所へ
-
- 16:00
- 終業