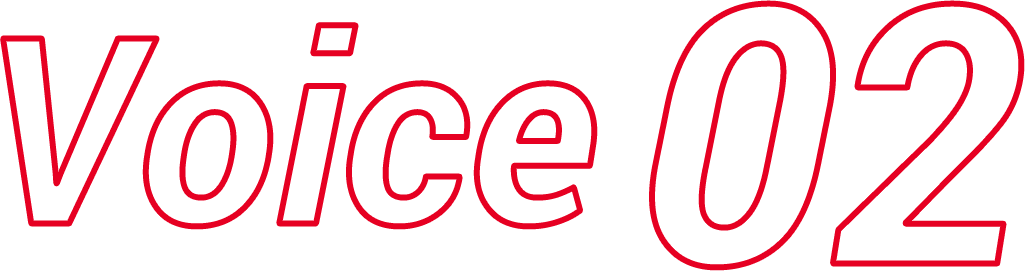
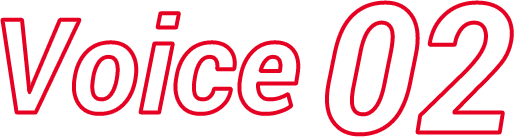
高機能製品カンパニー
地図に載るスケールの仕事を
無事故で成し遂げる。
- F.T
-
高機能製品カンパニー
堺工場 技術部 設備管理課2009年入社
※所属部署・役職、インタビュー内容は当時のものです
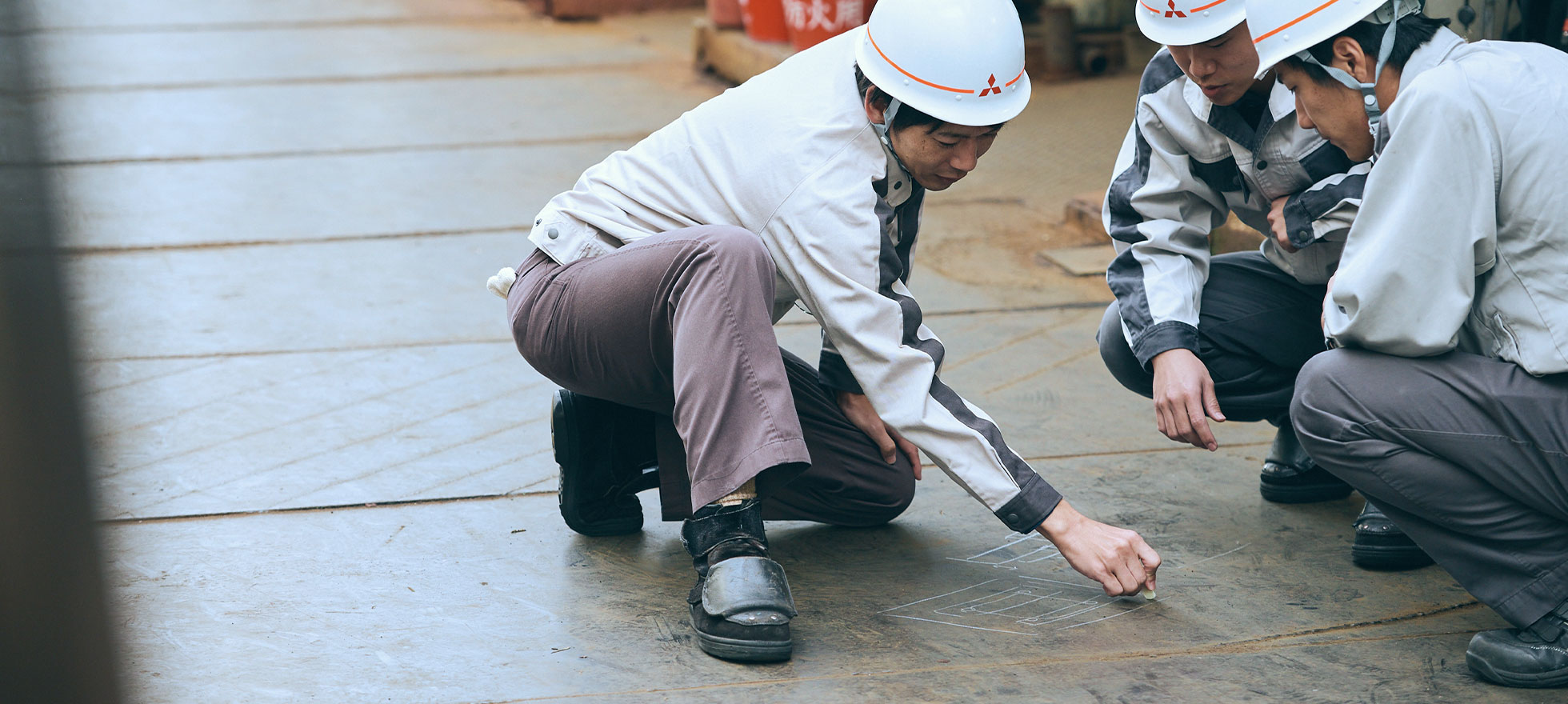
素材という幅広い領域で
常に新しいテーマに挑戦できる。
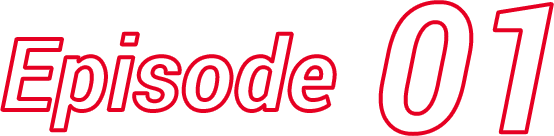
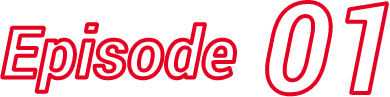
就職後の仕事として思い描いていたのは、機械工学の知識を活かして常に新しいテーマに挑戦し、社会に影響力のある仕事を成し遂げること。この想いが実現できる企業を求めて就職活動を始め、学内企業説明会でOBから紹介されたのが三菱マテリアルでした。興味を持った第一のポイントは、各種素材を生産するさまざまな設備に機械工学の知識が活かせること。第二に、手掛ける事業はいずれもビッグスケールな上、新規事業も積極的に展開していること。もちろん、業界のリーダーとして取り扱う各種素材が社会インフラの基盤を支え、企業としての安定性を確立していることにも魅力を感じました。
卒業後はUターン就職も一つの選択肢でしたが、全国に拠点を持つ三菱マテリアルに入社しました。最初の配属先は福島県にある銅製錬所である小名浜製錬(株)小名浜製錬所 保全動力課。初めての東北弁に慣れるまで少し苦労しましたが、先輩たちのサポートで、順調に社会人生活をスタートさせることができました。
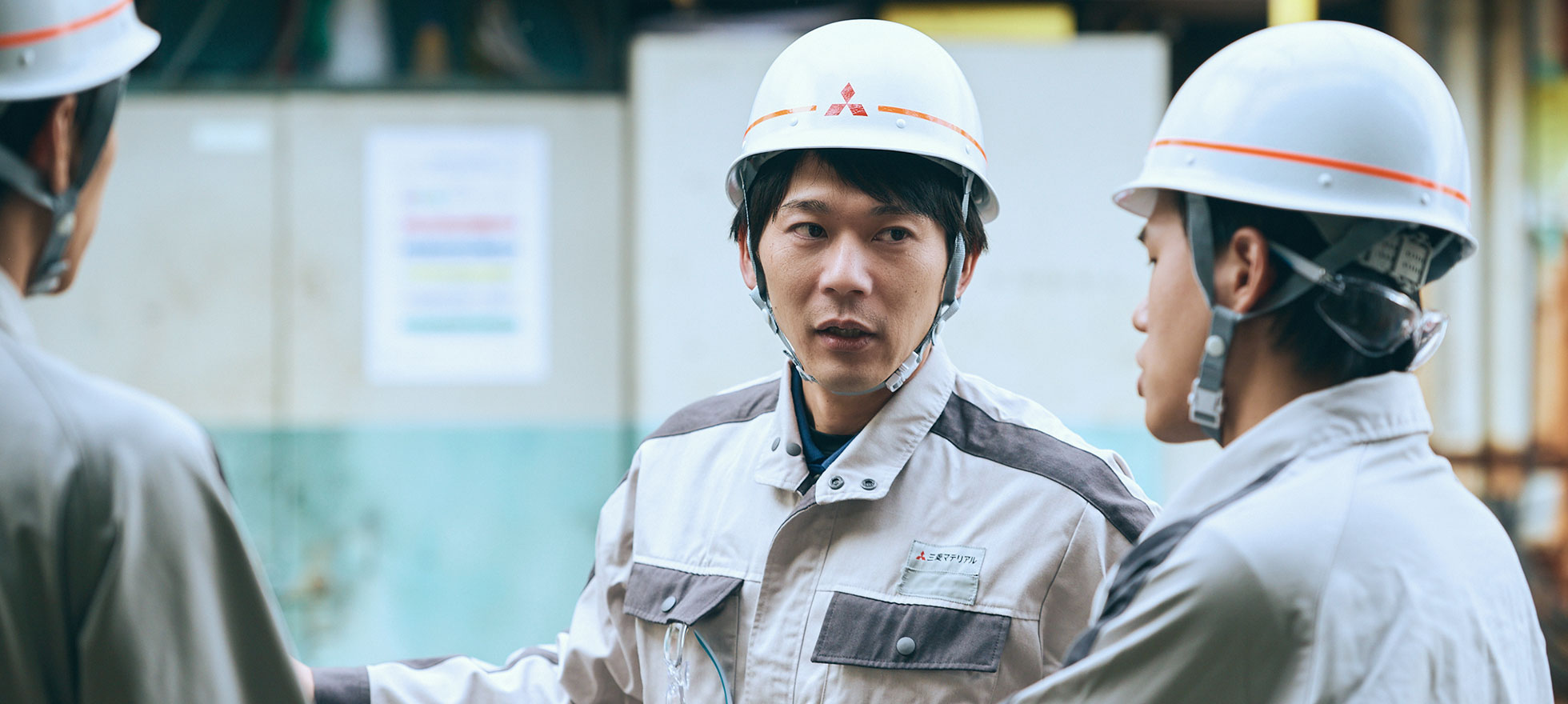
入社2年目の新規プロジェクトが
エンジニアリング力を高めるチャンスに。
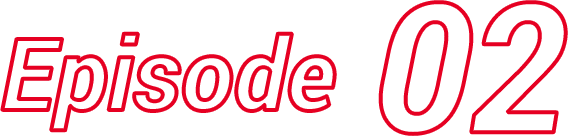
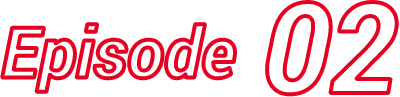
初の配属先は福島県いわき市にある小名浜製錬(株)小名浜製錬所 保全動力課でした。小名浜製錬所で生産しているのは、熱や電気の伝導率と圧延性に優れた純度99.99%という高品位の電気銅と製造工程で発生する副産物、電気銅を原材料とした銅の二次製品です。広大な敷地内では、銅生産の各プロセスを担う数々の建屋が存在感を示していました。その様子を見て、「生産設備設計のスキルを高めて銅生産全体の理解を深め、いずれは地図に載るようなプロジェクト全体をやり遂げたい!」という想いが湧いてきました。1年目の担当業務は電気銅生産の主要工程である銅電解を行う工場の設備管理でした。生産機器のメンテナンス等を通じて、生産設備の設計に必要な知識の習得に励みました。
2年目には銅電解の品質向上と生産量拡大を目指す工場設備の改修プロジェクトを、1年上の先輩と2人で担当することになりました。プロジェクトを進める上で重視したのは、製造現場とのコミュニケーション。設計側の視点から理想を追求するだけでなく、作業のしやすさなど現場の意向を設計に反映するためです。設計と生産現場の意向を擦り合わせ、議論を重ねて関係者全員が納得する生産設備環境の実現に取り組みました。半年後、頭の中で描いてきた生産設備がイメージ通りに稼働した時の感動は忘れられません。結果として、目標であった品質向上と生産量拡大を実現し、現場の方々から「よくやった!」と声を掛けていただいた時の達成感は格別でした。
また忘れられないのは、同時期に経験した東日本大震災の復旧プロジェクトです。被災後に避難場所から戻ってくると、海岸沿いにある小名浜製錬所は壊滅状態。銅鉱石の搬入口には、船舶が突き刺さっていました。一時は閉鎖も検討されましたが、製錬所は東日本における銅生産の大部分を担っていたことから政府機関の要請もあり、復旧に取り掛かることが決定。復興へのプレッシャーを感じる一方、「日本のインフラを支える銅生産は私たちスタッフの手にかかっている!」というプライドを胸に、全力で取り組みました。復旧工事には、三菱マテリアルの全事業所に加え、協力会社の方々も全国から応援に駆けつけ、1日あたりおおよそ1,000人強で作業を進めました。私は銅電解工場の復旧に向け、先輩たちと対応策を検討し、約200人を指揮して復旧作業を進めました。今でも目に焼き付いているのが、先輩たちの全体の状況を俯瞰し、何をどうすれば復旧作業がスムーズに進むのかを見極め、必要な資材や人員配置などをマネジメントする姿です。おかげであらゆる作業が迅速に進み、わずか6ヵ月程で操業復旧に漕ぎ着けることができました。
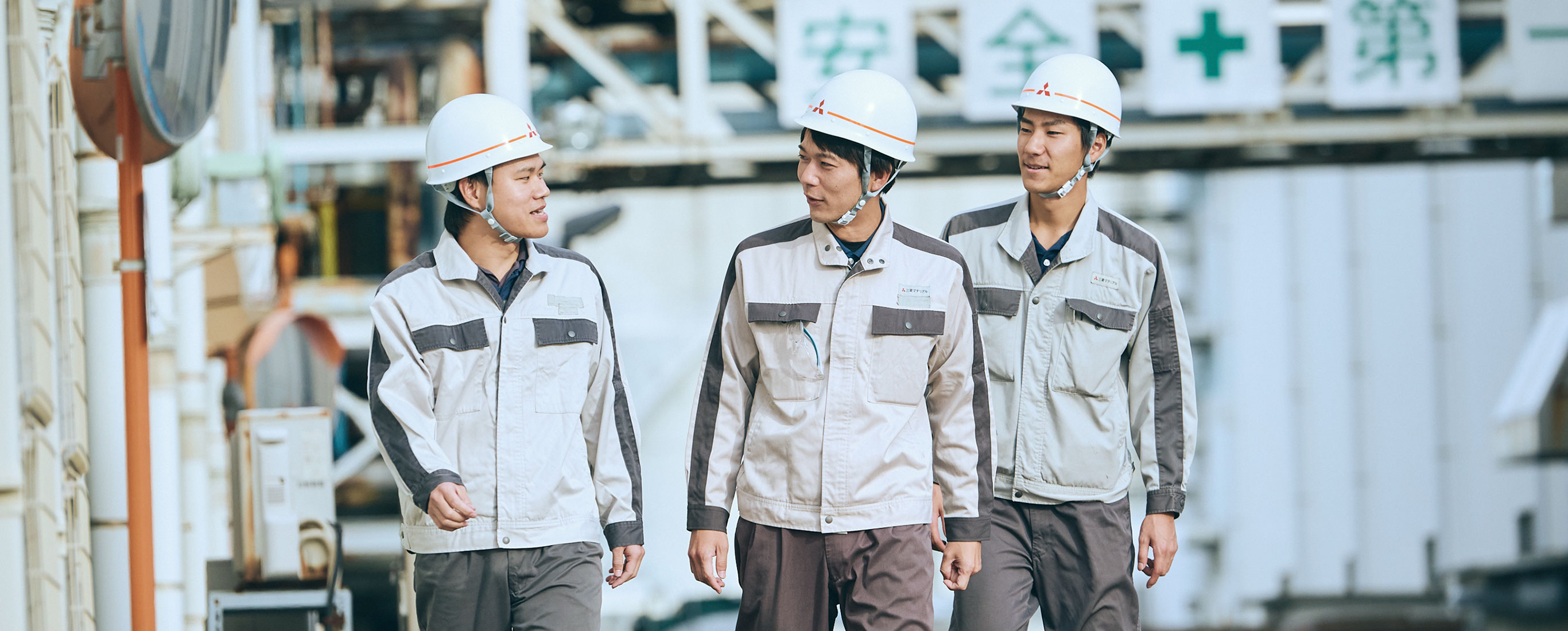
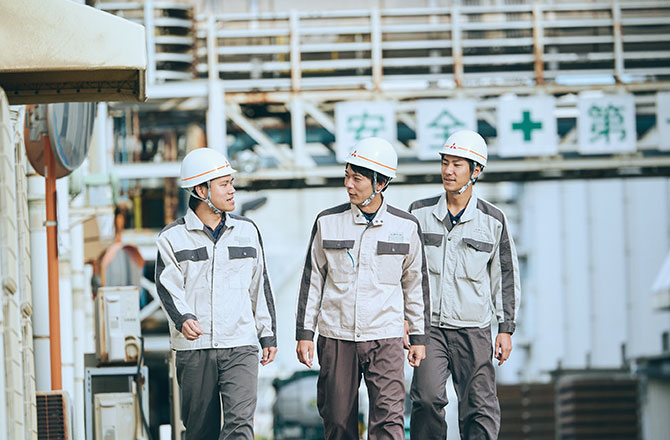
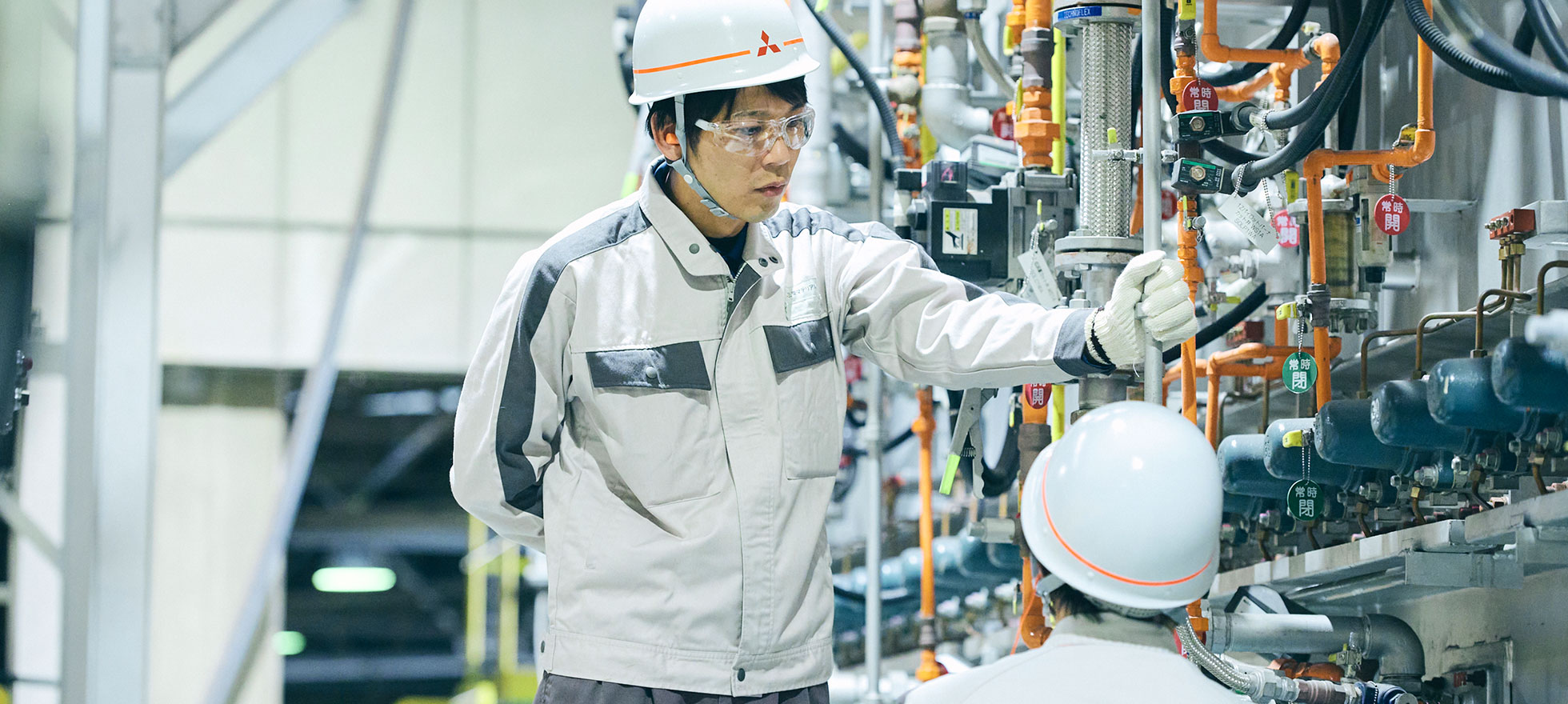
取り組んだ成果を地図で確認。
今後もエポックとなる仕事に挑戦。
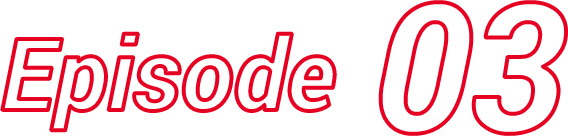
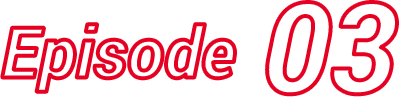
製錬所で取り組んだ新規プロジェクトと復旧工事の経験が、現在所属している堺工場でも役立っています。その一つが、先日落成した大規模プロジェクトです。数千トン規模で銅の生産能力を高めるため、コアとなる生産設備や電気設備、さらには社員駐車場の建設など、工場全域に関わる大規模工事を実施しました。私は起業認可後から担当者として参画。東日本大震災時の復旧工事で目に焼き付いた先輩たちの取り組みを参考にプロジェクト全体を見据え、掲げた目標を無事故で達成するために、各分野の責任者と協力しながら工事を推進。「地図に載るスケールの仕事をやり遂げる」という夢の一端を実現することができました。
現在は管理職として所属部門である設備管理課のマネジメントも担当。「楽しくやろう!」をモットーに、理想の組織づくりを進めています。さらに、工場の安全レベルを底上げするための体制づくりや、全社レベルで推進しているカーボンニュートラルを堺工場で実現するための計画策定にも取り組んでいます。今注力しているのが、新規プロジェクトの立ち上げで、複数のプロジェクトの準備を進めています。各プロジェクトにおいて無事故で目標を達成し、成果を地図で確認するのが今から楽しみです。

ある一日のスケジュール
-
- 8:00
- 出社後、今日のスケジュールをチェック
-
- 9:15
- 課内ミーティングを実施。前日のトピックス、計画されている工場内の行事、進行中の工事状況や今後の予定をメンバーに伝えて情報を共有
-
- 10:00
- 先日工事が完了した現場を巡視。機嫌よく稼働していることを確認
-
- 10:30
- デスクに戻り、メールチェックと伝票処理を実施
-
- 11:30
- マネージャーミーティングに参加し、工場幹部と各種情報を共有
-
- 12:00
- 昼休憩。スポーツを楽しむために福利厚生施設へ。最近は社内のバスケット人口が増えているが、私は工場のサークルでも楽しんでいるフットサルをプレイ
-
- 12:30
- 社員食堂で昼食
-
- 13:00
- 先月落成した新設備の実機試運転に立ち合い
-
- 16:00
- デスクに戻り、新規プロジェクトの実施に向けた資料を作成
-
- 18:00
- 終業